Burma Teak Engineered Plank
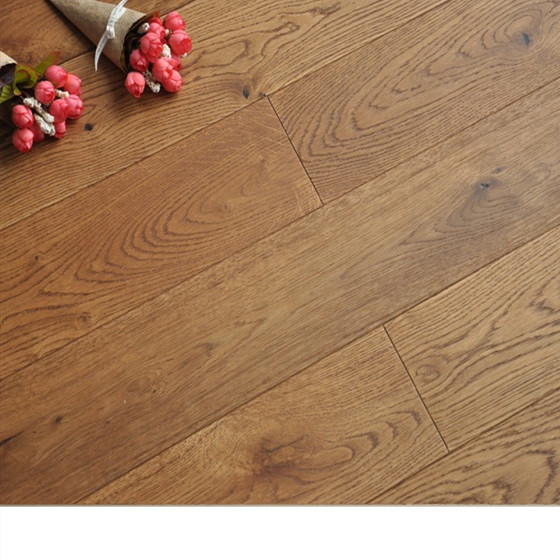
MM | INCH / FT |
---|---|
1860 x 148 x 14/3 | 6.1′ x 5.82″ x 0.55″ |
1900 x 190 x 15/4 | 6.23′ x 7.48″ x 0.59″ |
Structure | Eucalyptus Plywood Base |
Pre-Finish | UV Coating / Woca Oil |
Specification.
Length | Width | Thickness | Veneer | Grade |
---|---|---|---|---|
1860 mm | 148 mm | 14 mm | 3 mm | Natural / Rustic |
1860 mm | 148 mm | 15 mm | 4 mm | Natural / Rustic |
1900 mm | 190 mm | 14 mm | 3 mm | Natural / Rustic |
1900 mm | 190 mm | 15 mm | 4 mm | Natural / Rustic |
Strict QC System.
Under the control of ISO9001, ISO14001 and ISO14025, from material to the final product, each piece is processed through 49 working procedures and each procedure is controlled strictly by certain producing data. Especially for the procedures of kiln dry skills, environmental climates and pieces checking, which promise our floor with a stable and high quality.
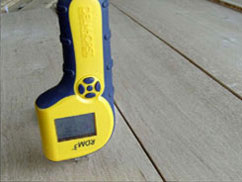
Moisture Checking
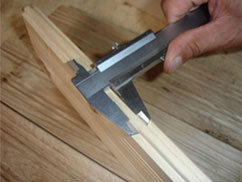
T&G Profile Checking
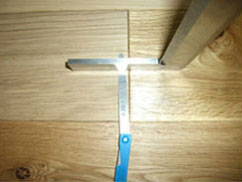
Glued Plywood
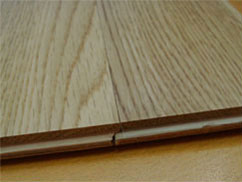
Square Edge
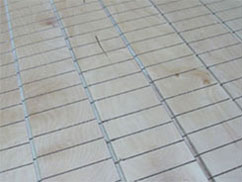
5.5mm Back Groove
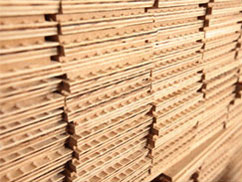
Moisture Checking
Packing & Loading
Specification | Pcs/Box | SQM/Box | Pallet/20FT | SQM/20FT |
---|---|---|---|---|
1860*148*14/3mm | 8 | 2.20224 | 12 | 1572.40 |
1860*148*15/4mm | 8 | 2.20224 | 12 | 1479.91 |
1900*190*14/3mm | 8 | 2.288 | 12 | 1577.71 |
1900*190*15/4mm | 8 | 2.288 | 12 | 1484.90 |
Packing Details
- Finished engineered wood floorings are packed with OEM export paper carton packaging.
- Flooring carton boxes are transmitted across through heat shrink plastic film to ensure waterproof packing system.
- Packaged cartoon boxes are neatly stacked on the pallets.
- Every corner and side are well protected by plastic anti-wet film and cardboard.
- Then the pallets are transmitted into the warehouse , waiting for loading.
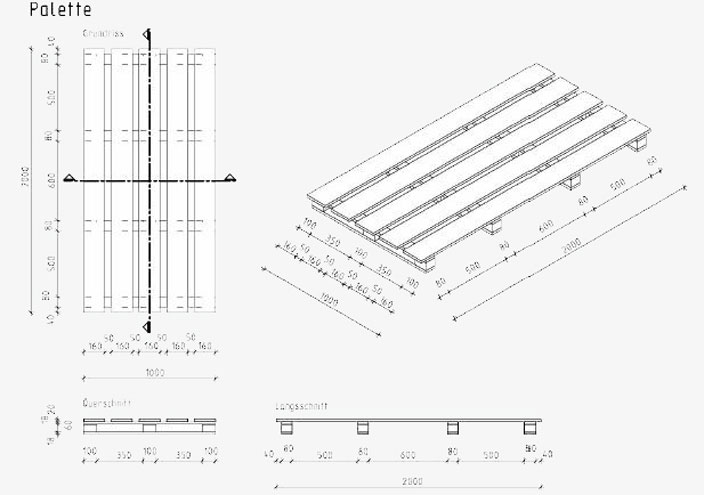
Container Loading.
- The Forklift carries pallets one by one, and then the pallets are loaded in the container in a row skillfully.
- Packaged cartoon boxes are neatly stacked on export pallets with all corner and sides well protected.
- When the container is filled with pallets, close the door and seal the container.
- Write and remember the Seal No. and Container Number
- Finally the lorry will take the container to the specified port.