Manufacturing
Golink differs from the average mill in that we value quality and innovation with a need to streamline the manufacturing process for our partners. Decades of experience, professional manufacturing center and good service mean we know what to look for in quality timber and produce the best outcome. Our process has been designed to get the most from harvest and maximise efficiency and quality in a safe manner.
The timber inside the kiln is connected to a computer to regulate temperature, humidity and wind speed. The computer only allows the drying process to stop once the timber has reached the optimum9±2% moisture content (MC).
At 9±2% MC, Golink has completed most of its shrinking. It is at this point that we stabilize our products to ensure that the users does not need to much acclimation before use.
The best time to produce our engineered teak flooring is from March to November when the oxidized teak color is at its peak in China.
The Core Of Our Business
Superior Material For Construction
Superior Material For Construction
Golink “hand selected” timber floorboards grade is much higher than others, every board is inspected prior to packaging in terms of grading, structure and stability.
The Core Of Our Business
Superior Material For Construction
Superior Material For Construction
Golink “hand selected” timber floorboards grade is much higher than others, every board is inspected prior to packaging in terms of grading, structure and stability.
A Proven Process For Premium Engineered Timber Flooring
A Proven Process For Premium Engineered Timber Flooring
Our manufacturing Approach is designed to help brands achieve their floorboards by valuing quality in every aspect. Our approach has proven to provide metamorphic results to our customer’s requirments, and our customers love it.
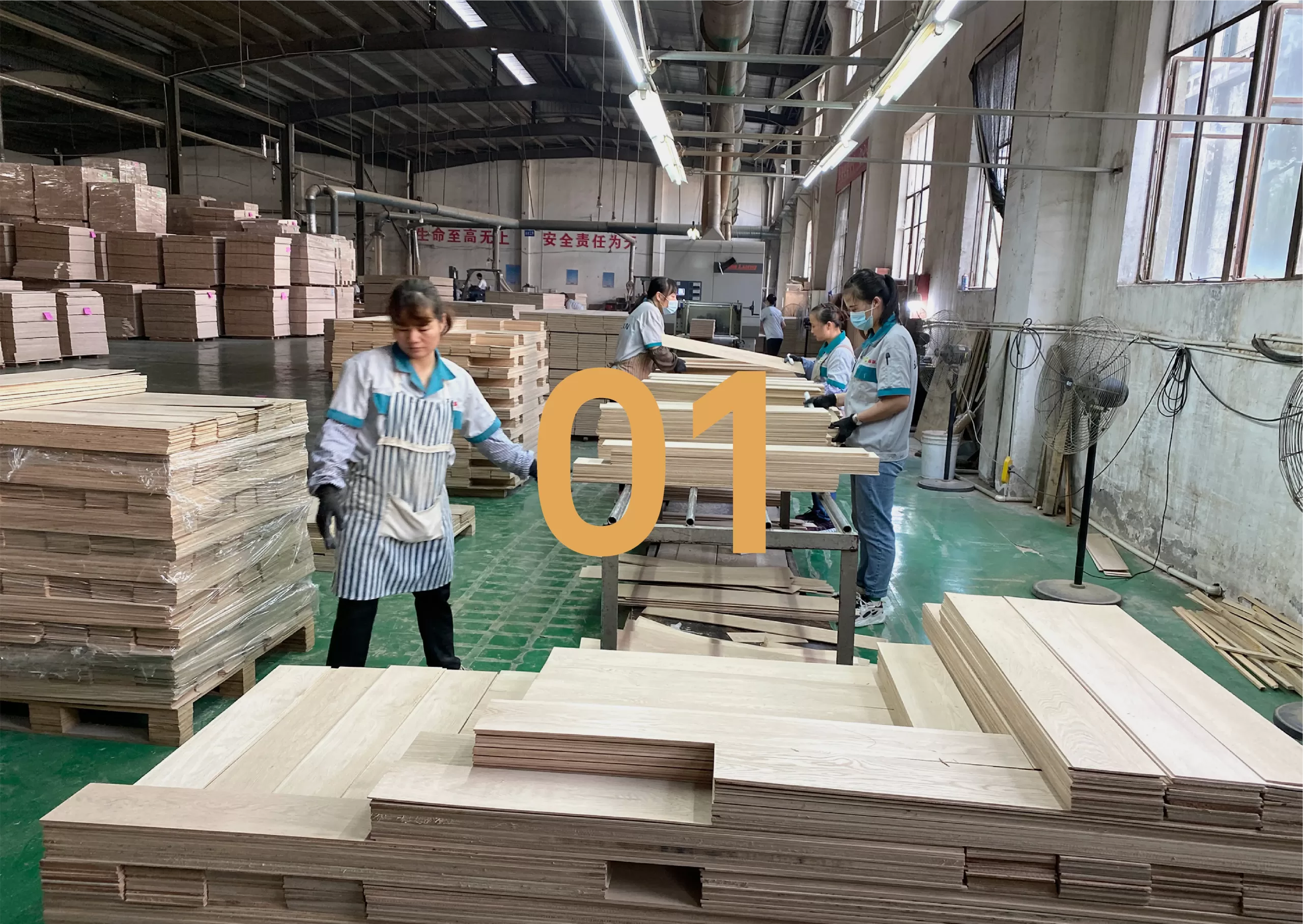
Hand Select Grading
Sorting timber lamella with Prime, Select, Natural, Character, Rustic Grades through grain, knots, sapwood, crack sizes etc.
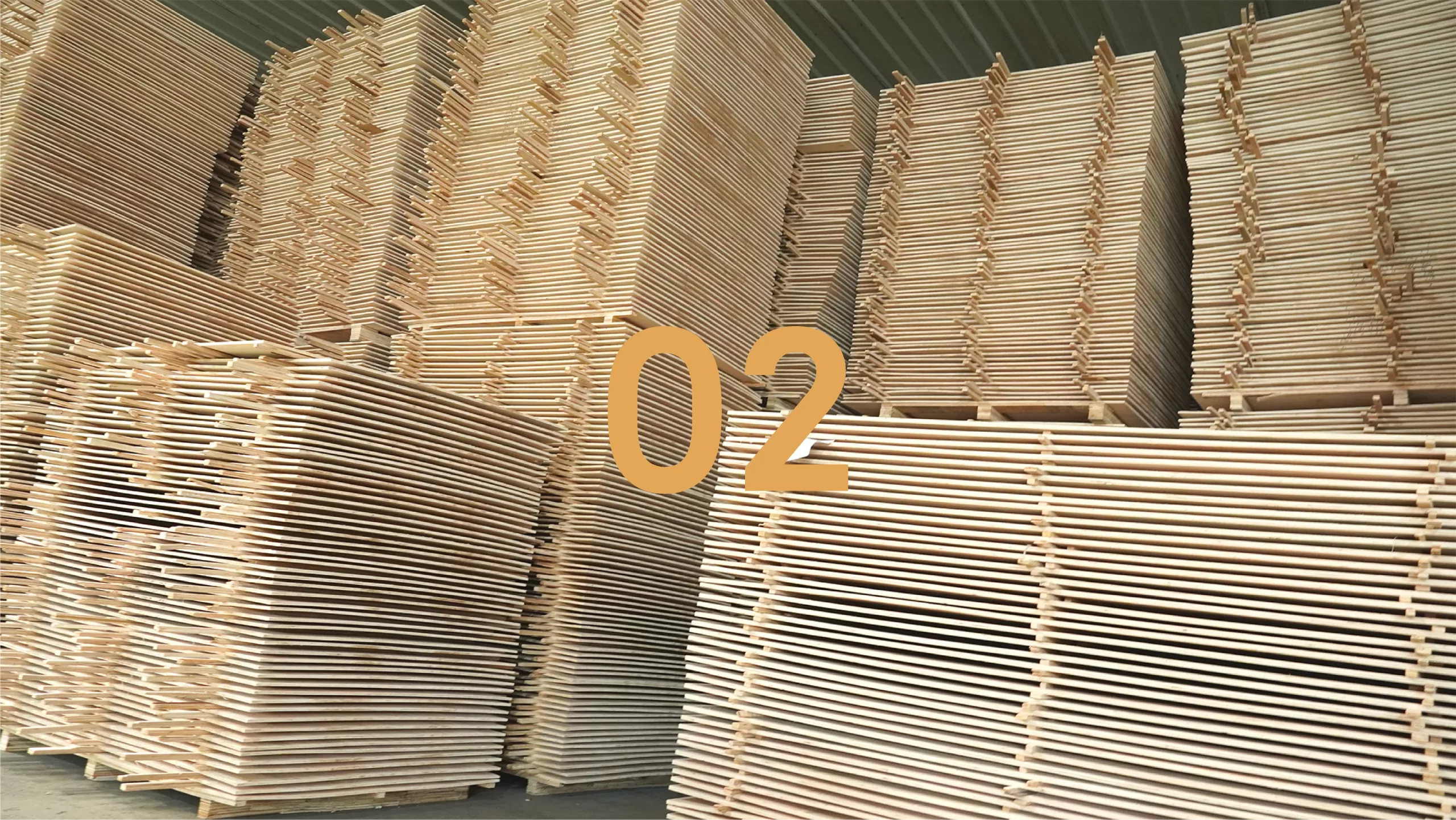
Kiln Drying
Racks of lamella and birch plywood inside the kiln to minimize internal stresses and reach the optimum 9±2% moisture content (MC).
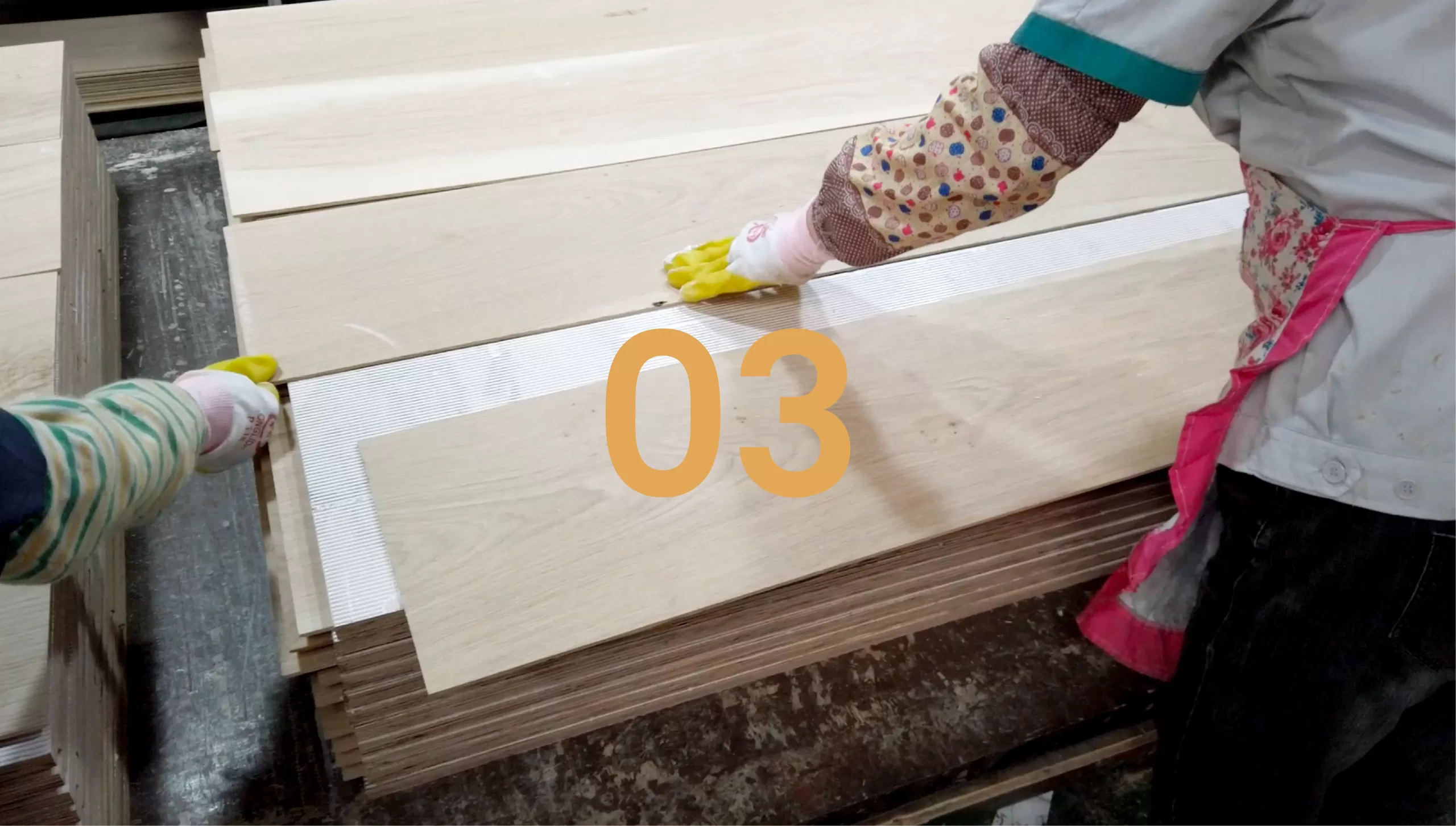
Attaching Lamella Plywood
Bonded lamella and plywood boards together with wood adhesive of Franklin Polymers ReacTITE EP-921.
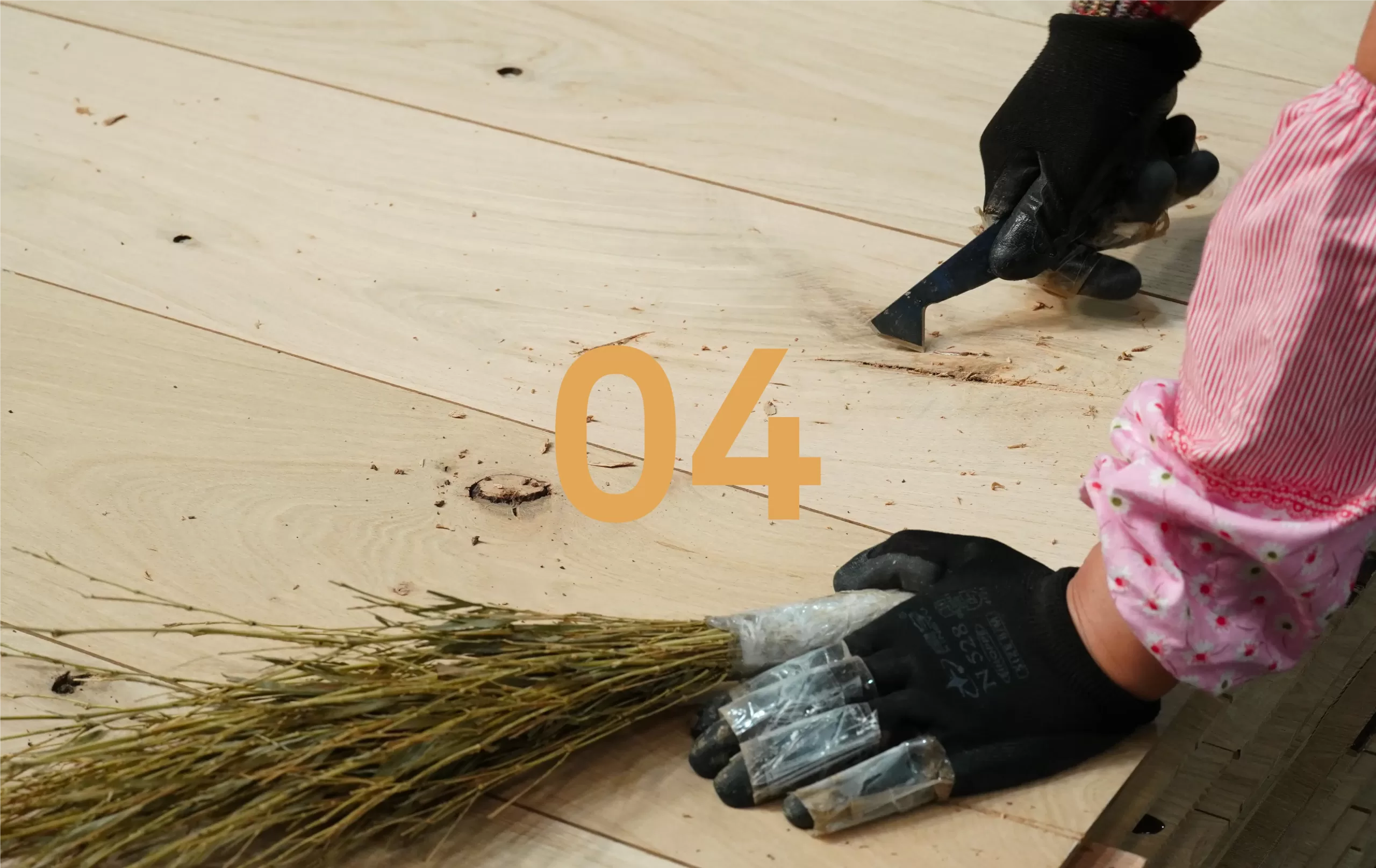
Repairing Knots Cracks
High quality Denalim epoxy resins used for knots and cracking repairing to get natural appearance.
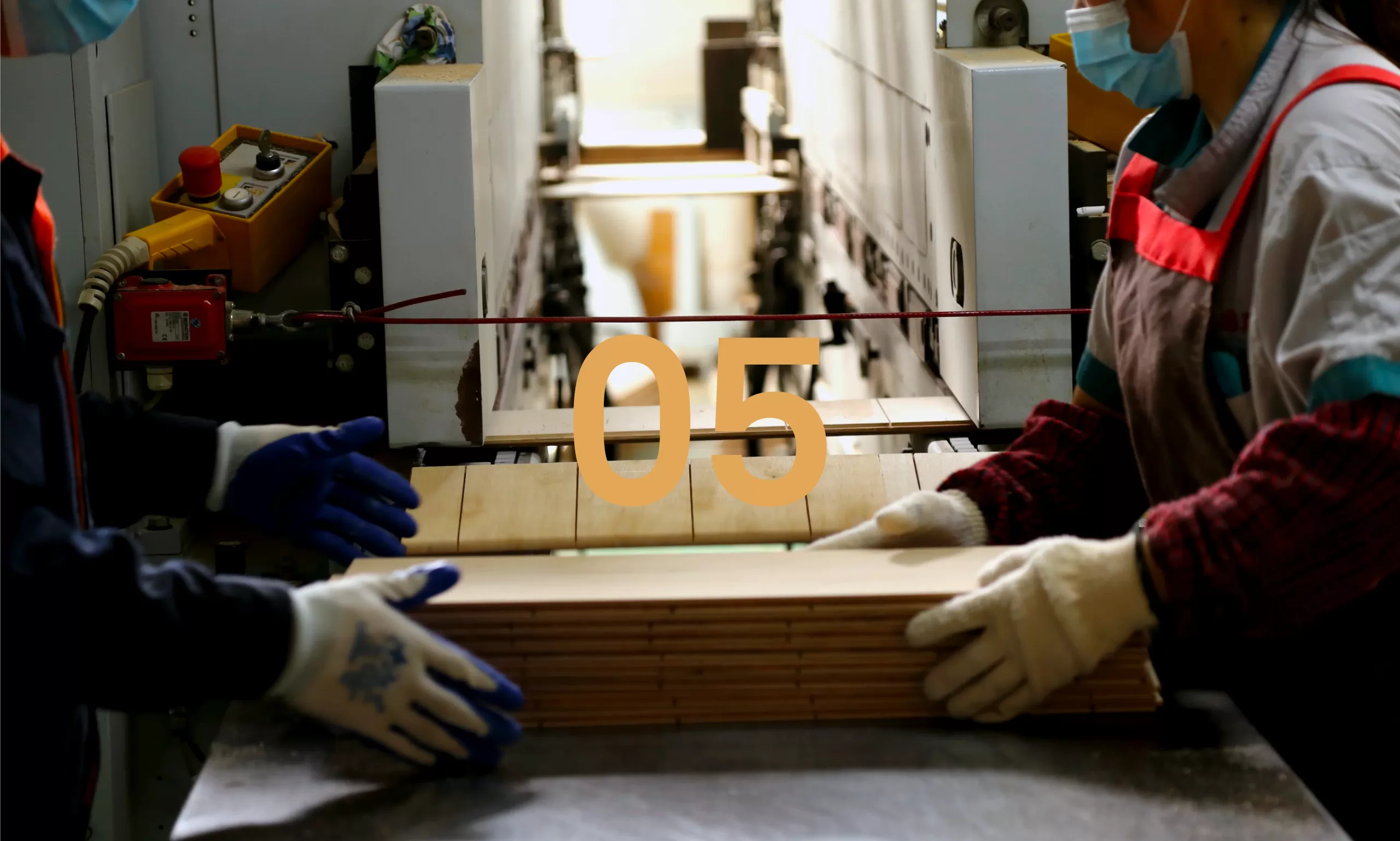
Precise tongue and groove achieved micro to full bevel through Germany Homag machine.
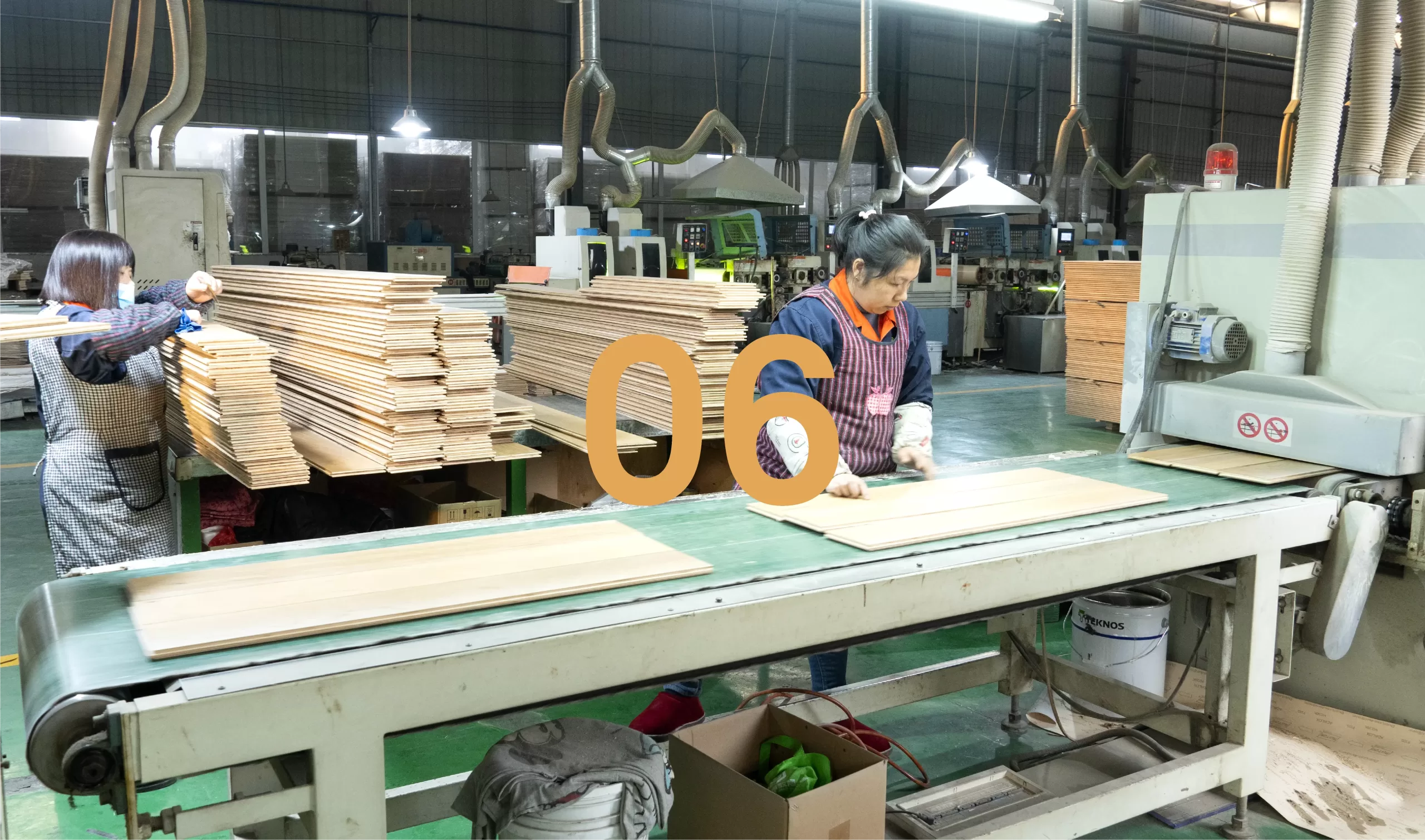
Achieving UV Lacquer & Oil
Unfinished floorboards get 7 coats of Germany Treffert UV-cured Lacquer, or Natural Oil finish.